

SOLIDWORKS users are lucky to have this feature. The result is usually very appealing and is difficult for many other CAD programs to execute. There are some rules to this as well but, once learned, it does become invaluable in tricky spots.
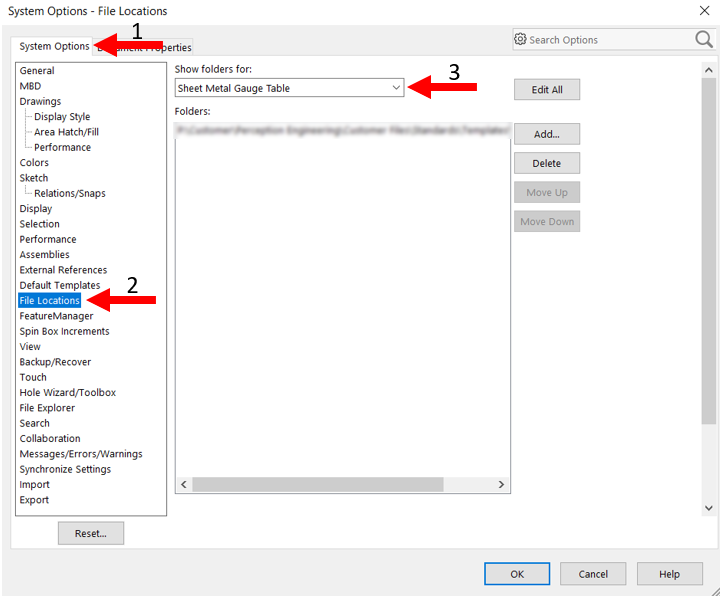
This comes in handy when trying to match up awkward angles. Edge Flange with profile adjusted.Īnother thing that I would like to point out on the Edge Flange is the ability to change the angle to match another surface. Some small rules apply here that most designers will figure out quickly.įigure 3.
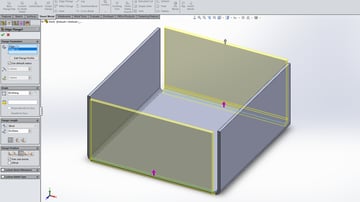
It can be any shape that is required as long as it is a closed profile that connects to the original edge. It doesn’t necessarily have to be a rectangle. One thing that often gets missed in the Edge Flange option is the ability to edit the flange profile. Designers can select flange positions that can move the flange location to the inside, outside, offset or to other less commonly used options that should be explored at your leisure. Designers can even select multiple edges that can be adjacent (by creating a mitered edge between the two) or located anywhere else on the same sheet metal body during this one operation. Of course, these can be overwritten if required.

This flange will inherit the radius and thickness parameters of the base flange. This same tool can be used to make a flat piece of sheet metal that one would use to add edge flanges and other useful sheet metal features.Įdge Flange (see Figure 3) can be used to add an attached wall to any sheet metal body. Options in basic Sheet Metal Base Flange/Tab. Not shown (scroll down in Property Manager) is an auto relief setting that controls how corners and relief cuts are handled.įigure 2. At any stage, these parameters can be overridden with drop downs and checkboxes that will correspond with input boxes to adjust for special cases. To use the gauge tables that were discussed earlier, one must check the “Use gauge table” box that opens up all selectable shop-approved gauges with their corresponding radii and the K-factor (or bend allowance), so that there is no worry of forgetting or mistyping anything. Drawing a simple profile and using the Base Flange/Tab tool will open up the options that can be used. There are many ways of doing this.Ī common favorite is sketching out the profile and using the Base Flange/Tab tool (see Figure 2) that is usually located first on the Sheet Metal ribbon. Next, let’s look at the basics of creating a sheet metal design. Filling this out with the help of your shop team really makes life easier. This setup builds consistency and accuracy out on the shop floor, which means less headaches for the designer.įigure 1. But once it is done and in place, it makes life easier for everyone in the company, especially if they all work off the same controlled file set. One may have to create a few of these files to fully utilize the entire catalog of a company. It must be done from thinnest to largest, and there can’t be duplicate thickness. Properly formatting the list of gauges is important. I personally use the K-factor version, but many may prefer bend allowance or go with a bend table. It is located in C:\Program Files\SOLIDWORKS Corp\SOLIDWORKS\lang\english\Sheet Metal Gauge Tables. The gauge table tool (see Figure 1) should be used as much as possible. Let’s go over a few.įirst off, let’s start with selecting material and gauge. SOLIDWORKS has some great tools to help with these. Regardless of all of those requirements, designers and engineers have to get the job done, and we have to get the job done fast in order to help our company succeed in producing new and innovative products. The sheet metal designer is often wearing two or three hats to accomplish all of these tasks. It requires many skills, trade secrets, compromises of design intent, machine capability knowledge and, often, patience in a fast-paced design environment. Oh, sheet metal, how one can love and be completely frustrated with the process at the same time! Sheet metal design is an intricate design process.
